Conveying and dosing specialists
65 YEARS OF EXPERIENCE AND EXPERTISE
Rotary Valves and Diverting Valves are used in breaking, dosing and pneumatic transport of powders and granules of any type, in the food, chemicals and plastics, lines of low, medium and high pressure.
Olocco avails itself of the very latest highly advanced technology in the design and production of its components.
A valid team is involved in ongoing research to renew and to improve the quality of its product range, thanks to a
modern CAD 3D system.
We use high-technology to produce valves and accessories for pneumatic transport and metering always in the vanguard in terms of technical specifications, quality and safety. Thanks to minimum tolerances and technical devices we are able to meet the specific needs of every type of product and customer.
(Mario Olocco)

VDL Groep acquires Italian family company Olocco
VDL Groep has acquired the Italian company Olocco.
Olocco is a manufacturer of socalled rotary valves and industrial diverting valves.
With the company, located in Fossano (about 75 kilometres south of Turin), in its ranks, VDL expects to further strengthen its production and sales activities in the Foodtech domain, one of the ‘five worlds of VDL’.
VDL Industrial Products from Eindhoven, one of VDL’s operating companies, has been the exclusive representative in the Benelux of the products of industry partner Olocco since the early 1990s. Since then, Olocco has been selling the products of VDL Industrial Products in its home country Italy.
Like Olocco, VDL Industrial Products produces components for industrial installations for the handling and storage of dry materials (powders and granulates), such as rotary valves.
These valves dose dry materials from a storage system, like a silo, to a transport or other system or into a machine.
Diverting valves are, for example, built-in a pneumatic conveying or suction transport system through which dry materials are guided in a controlled manner to various machines or parts of industrial systems.
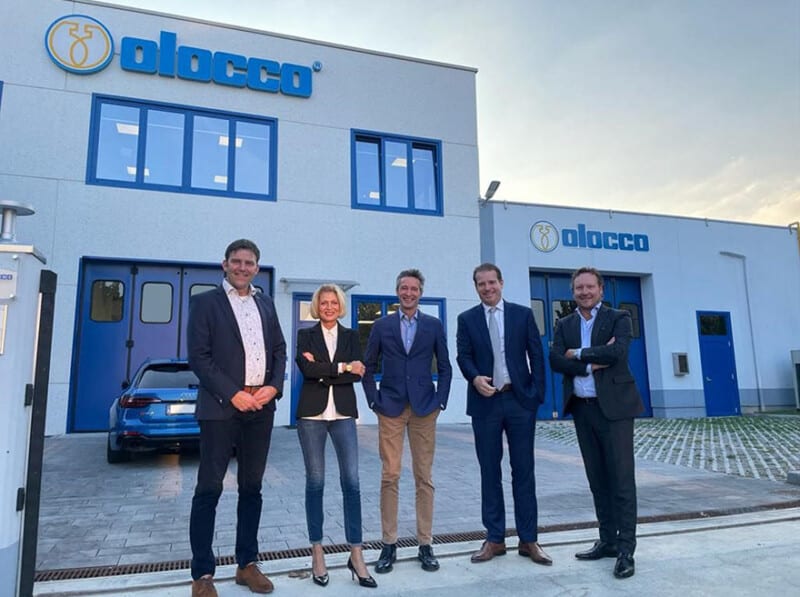
Caption: The Olocco building in Fossano, Italy, with (from left to right): Carlos Ooijen (Managing Director of VDL Industrial Products), Andreana Olocco (Head of Administration Olocco), Umberto Olocco (Managing Director of Olocco), Willem van der Leegte (President & CEO of VDL Groep) and Rémi Henkemans (Senior Vice President of VDL Groep).
FOOD COMPATIBILITY
For the particular construction the several type of rotors and the minimum
tolerances, it ensures excellent airlock and good flowing of the product in pneumatic conveying lines.
In compliance with the provisions of the EC regulation nr. 1935/2004 concerning materials and objects intended to come into contact with food products
(MOCA), and to the EC regulation nr.2023 / 2006 on good manufacturing practices of materials and objects intended to come into contact with food.

For us, being among the leading companies in the Movement and Dosing sector is a source of pride and satisfaction.
For our work we need great preparation, precision and constant updating and the passion that we have for it, allows us today to exceed the expectations of the most demanding customers
UPH and UPH/sr
STAINLESS STEEL ROTARY VALVE
Quick disassembly

The “UPH” rotary valve type is particularly suitable for metering and pneumatically conveying of granular, flaky or ground products.
Thanks to its sturdy construction and flanging unified according to UNI PN10 standard (DIN 2576ND10) it is suitable for use in both heavy industry and in the chemical and plastic industrial fields.
The high quality of used materials, the parts in contact with the product in AISI316L stainless steel, the complete external bearings with PTFE gland packing and the good finishing make very easy the use of the rotary valve “UPH” in several markets; food and feed stuff industry, for example.
The “UPH-SR” rotary valve is the version equipped with a quick disassembly system with extraction bars, a completely removable rotor and internal surfaces polished and connected to meet the highest cleaning standards.
It is particularly suitable in those fields where the manufacturing processes require a frequent cleaning of the rotor and inside the body.
Thanks to the quick disassembly, time is saved and the time-work factor optimized.



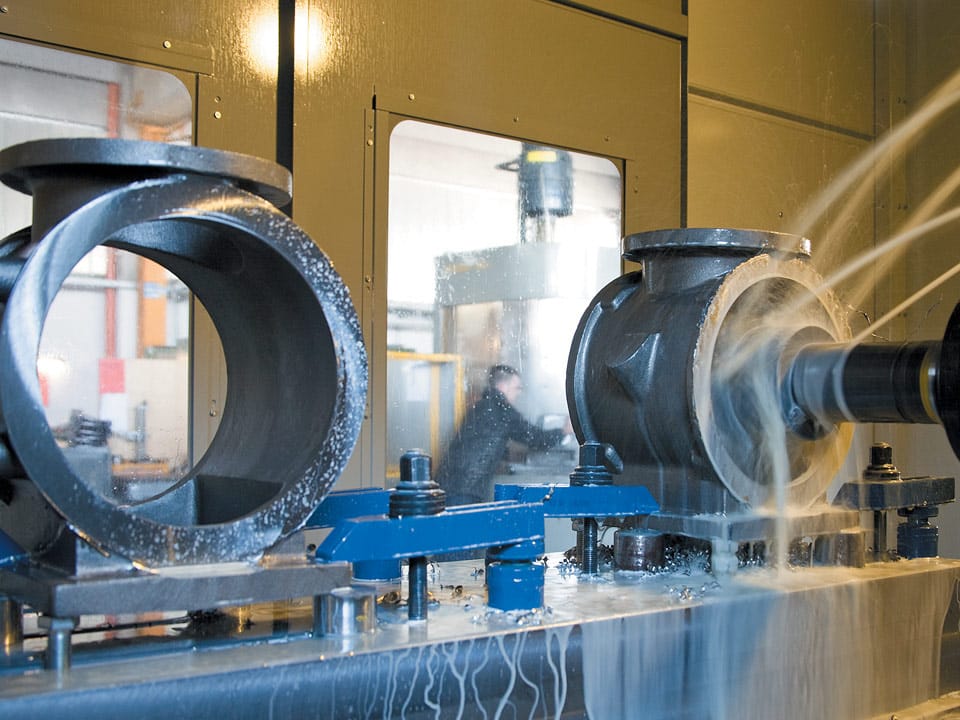